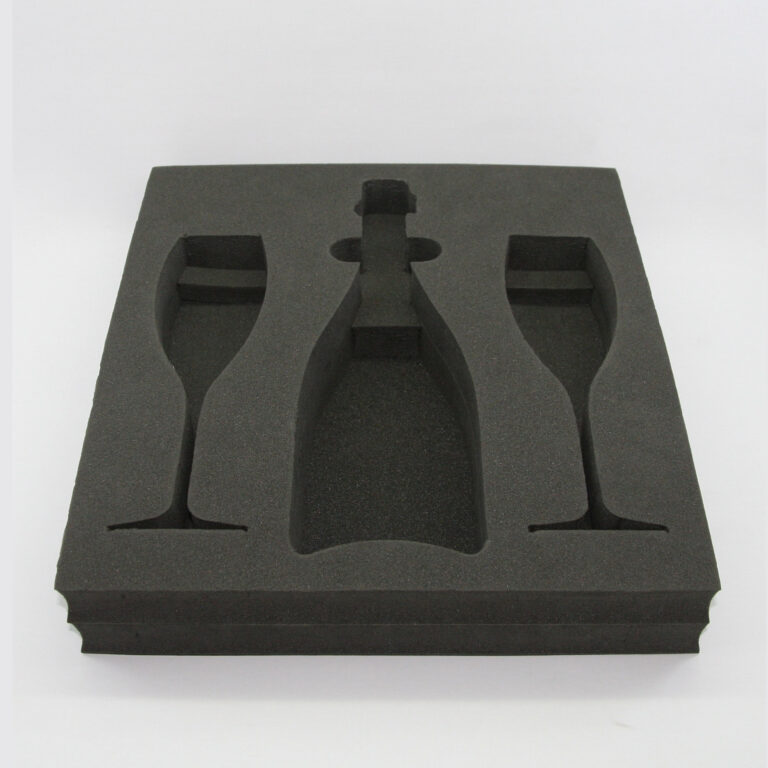
Foam packaging inserts have become a crucial element in ensuring product safety during storage, transportation, and handling. Their versatile, protective properties make them an ideal choice for industries ranging from electronics to fragile glassware. In this guide, we will explore foam packaging inserts, their benefits, types, applications, and tips for choosing the best solution for your business.
What Are Foam Packaging Inserts?
Foam packaging inserts are custom-made protective components designed to secure items within boxes or containers. These inserts are crafted from various foam materials to cushion, support, and prevent movement during transit. The adaptability of foam allows manufacturers to create tailored solutions for products of all shapes and sizes.
Key Benefits of Foam Packaging Inserts
1. Superior Protection
Foam inserts offer unparalleled protection against impacts, vibrations, and drops. By absorbing shocks, they ensure that delicate or valuable items remain intact during transportation.
2. Customization
These inserts can be precisely cut to fit your product dimensions, ensuring a snug fit. This minimizes movement and provides optimal security for your items.
3. Lightweight Design
Foam materials are incredibly lightweight, reducing overall shipping weight and costs while maintaining durability and effectiveness.
4. Cost-Effective
By preventing damage and reducing returns or replacements, foam inserts save businesses significant costs in the long term.
5. Eco-Friendly Options
With increasing environmental concerns, many foam inserts are now made from recyclable or biodegradable materials, offering sustainable packaging solutions.
Types of Foam Packaging Inserts
Choosing the right type of foam insert depends on your product’s specific needs. Here are some commonly used foam materials:
1. Polyethylene (PE) Foam
- Durable and Rigid: Ideal for heavy-duty applications.
- Water-resistant: Suitable for products exposed to moisture.
- Common Uses: Electronics, automotive parts, and industrial machinery.
2. Polyurethane (PU) Foam
- Soft and Flexible: Provides cushioning for delicate items.
- Shock Absorption: Excellent for products prone to impacts.
- Common Uses: Medical equipment, glassware, and musical instruments.
3. Expanded Polystyrene (EPS) Foam
- Lightweight: Perfect for reducing shipping costs.
- Moldable: Easily shaped for specific products.
- Common Uses: Food packaging, appliances, and retail products.
4. Cross-Linked Polyethylene (XLPE) Foam
- High-Density: Offers superior protection and chemical resistance.
- Aesthetic Finish: Often used for luxury items.
- Common Uses: Cosmetics, jewelry, and high-end electronics.
5. Anti-Static Foam
- Electrostatic Protection: Prevents damage to sensitive electronics.
- Customizable: Available in various densities.
- Common Uses: Circuit boards, computer components, and telecommunications devices. more
Applications of Foam Packaging Inserts
1. Electronics and Technology
Foam inserts safeguard fragile and expensive gadgets like smartphones, laptops, and circuit boards, ensuring safe delivery to customers.
2. Medical and Pharmaceutical
Custom foam inserts are used to protect delicate medical devices, instruments, and lab equipment during shipping.
3. Automotive Industry
Foam inserts are vital in transporting automotive parts like engines, mirrors, and delicate components without damage.
4. Retail and E-Commerce
Whether shipping perfumes, cosmetics, or glassware, foam inserts enhance the unboxing experience while ensuring product integrity.
5. Food and Beverage
Temperature-sensitive items, such as frozen goods or wine bottles, benefit from the insulation and cushioning properties of foam inserts.
How to Choose the Right Foam Packaging Inserts
Selecting the ideal foam insert involves understanding your product’s needs and packaging requirements. Consider the following factors:
1. Product Dimensions
Accurate measurements ensure a snug fit, reducing the risk of movement and damage.
2. Foam Material
Choose a foam type that aligns with your product’s weight, fragility, and sensitivity. For instance, anti-static foam is crucial for electronics.
3. Environmental Impact
Opt for eco-friendly foam materials if sustainability is a priority for your brand.
4. Cost Efficiency
Balance protection with budget considerations by selecting the right density and type of foam for your application.
5. Aesthetic Appeal
For premium products, consider foam inserts with a clean, professional finish that enhances customer perception.
Custom Foam Packaging Inserts: The Process
1. Design and Prototyping
Collaborate with a packaging expert to design inserts tailored to your product with custom made packaging boxes. Prototypes ensure accuracy before mass production.
2. Material Selection
Choose the foam material that best suits your product’s requirements, balancing protection and aesthetics.
3. Cutting and Fabrication
Advanced cutting techniques, such as die-cutting or water-jet cutting, ensure precision and consistency in foam insert production.
4. Quality Control
Rigorous testing ensures the foam inserts meet durability and protection standards.
Tips for Maximizing Foam Insert Effectiveness
- Test Fit: Always test inserts with your product to ensure proper alignment and security.
- Combine Materials: Use a mix of foam types for added protection, such as pairing anti-static foam with durable PE foam.
- Invest in Quality: High-quality foam materials reduce long-term costs by minimizing product damage.
- Communicate with Suppliers: Provide detailed product specifications for accurate customization.
Conclusion
Foam packaging inserts are an indispensable solution for businesses aiming to protect their products and enhance customer satisfaction. Their versatility, cost-effectiveness, and customizable nature make them a preferred choice across industries. Whether you are shipping delicate electronics or luxury goods, foam inserts provide the peace of mind that your items will arrive in perfect condition.