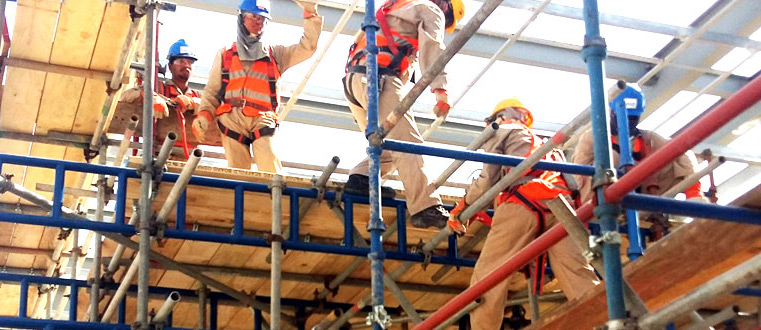
The cuplock scaffolding method is widely used worldwide due to its simple setup, quick assembly, and cost-efficiency, made possible by its unique locking mechanism. In the construction sector, this system remains highly popular.
The Cuplock Scaffolding System includes modular components, mainly pre-engineered horizontal and vertical elements, which users assemble systematically to form temporary structures. This system is simpler and faster to use than conventional scaffolding systems. In contrast to pipes and fittings, the Cuplock system is easy to install, saving time and lowering costs.
Builders, repair teams, and maintenance crews rely on cuplock scaffolding for various applications, including façade scaffolding, birdcage structures, loading and unloading areas, curved structures, staircases, support frameworks, and mobile towers. It enables tasks like painting, flooring, plastering, and finishing work to be done efficiently and comfortably without compromising the primary structure.
Despite its durability, assembling Cuplock Scaffolding is straightforward. The system’s unique node locking mechanism lets users secure four horizontal tubes to standard or vertical tubes with a single hammer strike. The lower stationary cups, welded at intervals of half a meter, hold the sliding top cups. The sliding cups engage the ledger blades and twist into place, ensuring a secure fit without clips, wedges, or bolts.
Key Features of the Cuplock Scaffolding System:
- Efficient: Simple to assemble with only four component fastenings.
- Lightweight: Made from 3.2mm high-grade steel, it is 20% lighter than standard 4mm scaffolding tubes.
- Cost-effective: Consists of only three main components.
- Rapid: Increases efficiency by up to 30% over conventional scaffolding.
- Resilient: Hot-dip galvanization requires less maintenance and ensures longevity.
- Versatile: With 500mm cup intervals on the verticals, it adapts well for circular structures, birdcages, and staircases.
- Adjustable: Provides spans from 0.6m to 3.0m using boards or battens.
Cuplock scaffolding manufacturers provide adaptable, efficient systems prioritizing safety and reliability in construction and manufacturing projects.
Cuplock Scaffolding Maintenance Recommendations
Proper maintenance is crucial to ensure the safety and longevity of cuplock scaffolding on construction sites. Regular maintenance preserves the scaffolding’s structural integrity and protects workers who rely on it daily. Follow these essential maintenance steps to keep your cuplock scaffolding in optimal condition:
- Regular Inspections: Schedule frequent inspections to examine the scaffolding for wear and tear, including signs of rust, warping, or cracks. Carefully inspect cuplock connections, ensuring they are secure and free from any debris that could interfere with their function.
- Routine Cleaning: Dirt, dust, and debris can build up on scaffolding, affecting its appearance and safety. Set up a regular cleaning routine, particularly after heavy rain or storms, and use appropriate cleaning agents that won’t damage the scaffolding material.
- Proper Storage: When not in use, store cuplock scaffolding parts in a dry, secure location to protect them from environmental damage. Proper stacking also helps prevent any deformation or warping of components over time.
- Immediate Repairs: Address any damage discovered during inspections promptly. This may involve replacing worn parts or reinforcing areas that have weakened. Tackling minor issues early on helps prevent them from escalating into significant safety risks.
By implementing these maintenance practices, you can maximize the performance and safety of your cuplock scaffolding, ensuring it remains a reliable and long-lasting asset for your construction projects.
Bottom Line
Cuplock scaffolding has proven to be an invaluable asset in construction, thanks to its efficiency, adaptability, and cost-effectiveness. Its unique locking mechanism and modular design streamline setup, making it a preferred choice for a wide range of applications. By following proper maintenance practices, users can extend the system’s lifespan and ensure the safety of all personnel on-site. Whether you’re an experienced manufacturer or a new contractor, understanding and implementing the benefits of Cuplock scaffolding can lead to safer, more efficient projects.